Faucet Manufacturing Machines
are specialized equipment designed to efficiently produce various types of faucets for residential, commercial, and industrial use. These machines automate several key stages of the production process, ensuring consistency, accuracy, and high output.
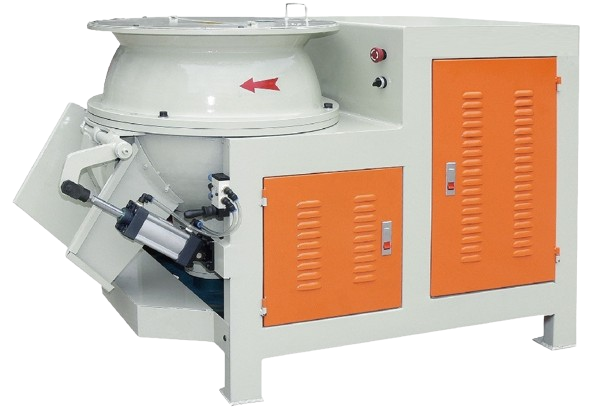
Sand Mixing Machine
The spherical rotary sand mixer blends quartz sand, binders, and additives into high quality molding sand through a tumbling action. As the drum rotates, the sand mixture is lifted and dropped repeatedly to achieve thorough mixing. The well-blended sand flows smoothly into core boxes or molding machines to produce casting molds and cores with tight, dense surfaces. This results in castings with good surface finish, dimensional accuracy, and easy core removal. Rotary sand mixers are commonly used in foundries casting iron, steel, aluminum, and bronze parts for applications such as automotive components, plumbing fixtures, hardware, valves, and more. Their efficient mixing action allows foundries to produce small or large volumes of quality sand molds and cores.
SEMI AUTOMATIC CORE SHOOTER MACHINE
The heat box core shooter is a semi-automatic vertical parting machine used for small-scale core production. This simple, affordable core shooter requires manual loading of the core box and unloading of finished cores. The main components include the mechanical assembly, pneumatic system, and electrical controls. To operate, the operator places the core box into the heating chamber, which softens the sand mix. The pneumatic rams then compact the sand into the core box cavity. After venting, the box opens and the finished core is ejected. The heat box core shooting process is commonly applied in aluminum and copper foundries to produce small batches of various shaped cores with low strength requirements. The manual operation makes this an ideal low-cost option for small foundries rather than investing in fully automated core machinery.
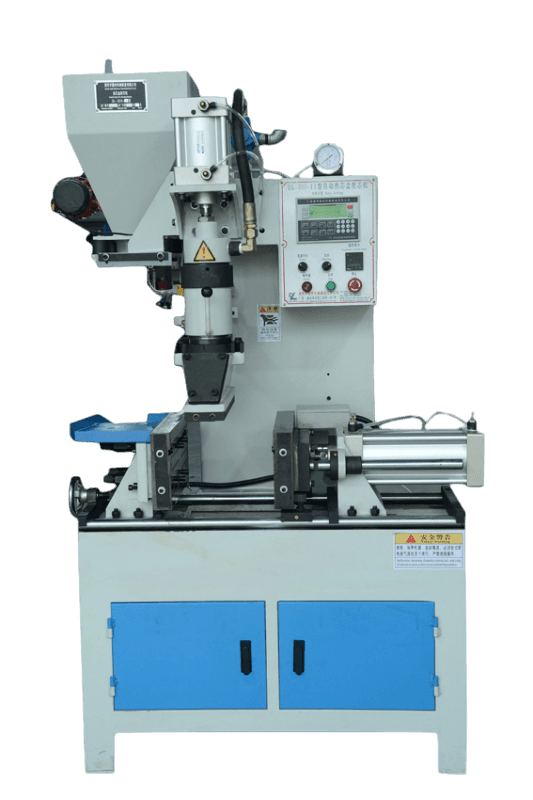
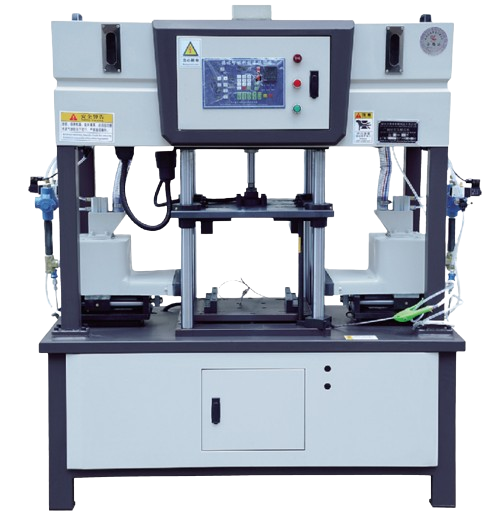
AUTOMATIC DOUBLE-HEAD CORE SHOOTING MACHINE
The automatic dual-head core shooting machine is a fully automated hot box core making system. It combines mechanical clamping, heating chambers, sand filling, pneumatic rams, electrical controls, and PLC programming into one integrated unit. Key components include a robust frame, mold clamping mechanism, insulated outer covers, sand distribution system, pneumatic valve banks, motor starters, and an industrial touchscreen. In operation, the machine sequentially clamps each core box, fills it with pre-heated sand, compacts the sand into the cavity, strikes off excess material, and opens to eject the finished core. The automatic cycling between two heated shooting heads allows high-volume continuous core production with minimal manual intervention. The programmable controls and identification system enable flexible production of multiple core sizes and shapes. This advanced automation makes the dual-head core shooter ideal for medium to large foundry operations.
GRAVITY CASTING MACHINE
This innovative brass casting machine is designed for easy operation and affordability. It utilizes a human-machine interface with real-time process monitoring, menu-driven controls, and intelligent parameter storage. The independent PLC system enables a wide range of settings, troubleshooting, and low maintenance. In operation, the upper and lower mold halves clamp and rotate to achieve even pouring and prevent defects like cold runs. The cooling fluid is a mixture of graphite powder and water, which coats the sand cores for clean demolding. The graphite withstands high temperatures without dissolving in water. This unique gravity casting design is ideal for small-volume brass casting. The intelligent controls, automated operation, and graphite-based cooling deliver high yields of quality castings. The simplicity maximizes uptime while minimizing the labor and costs associated with brass production.
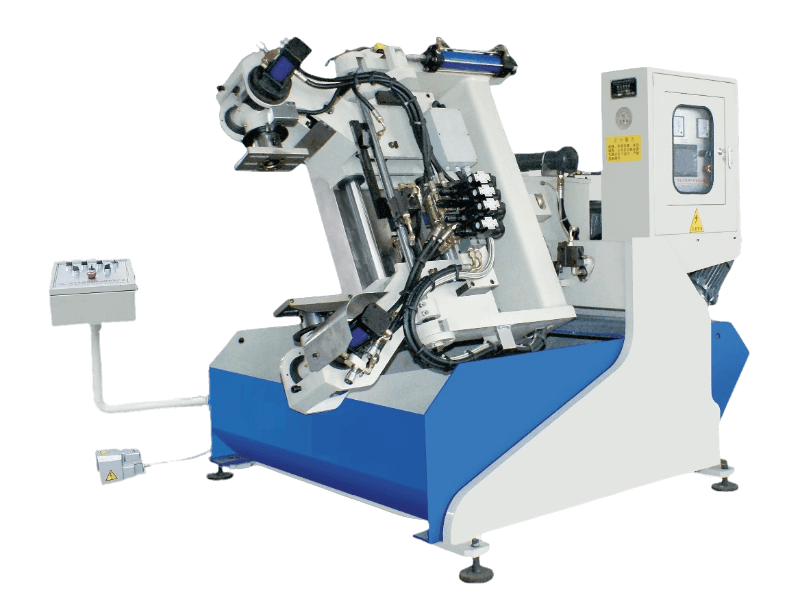
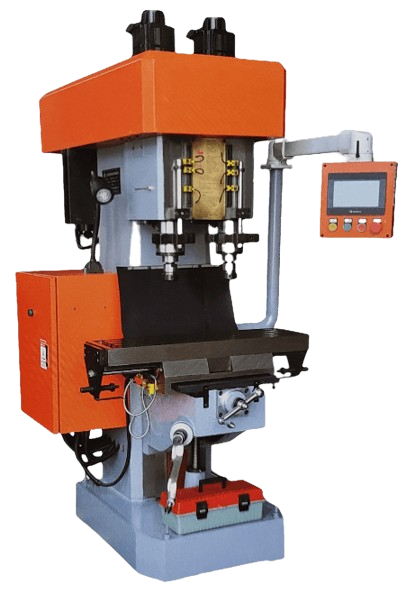
Servo Double Spindles Compound Machine
The tapping process utilizes servo motors for enhanced accuracy and precision. Minimal operators required, increased productivity a single worker can oversee multiple units simultaneously. Incorporates a PLC-based automation system, ideal for high-volume batch production. Drilling and tapping operations can be performed in one consecutive sequence. The guide rails are hardened through ultrasonic quenching to withstand high-speed machining. Pneumatic clamps provide rapid, convenient fixturing of parts.
Special Purpose Machines(SPM)
3-Spindle SPM
4-Spindle SPM
6-Spindle SPM
8-Spindle SPM
12-Spindle SPM
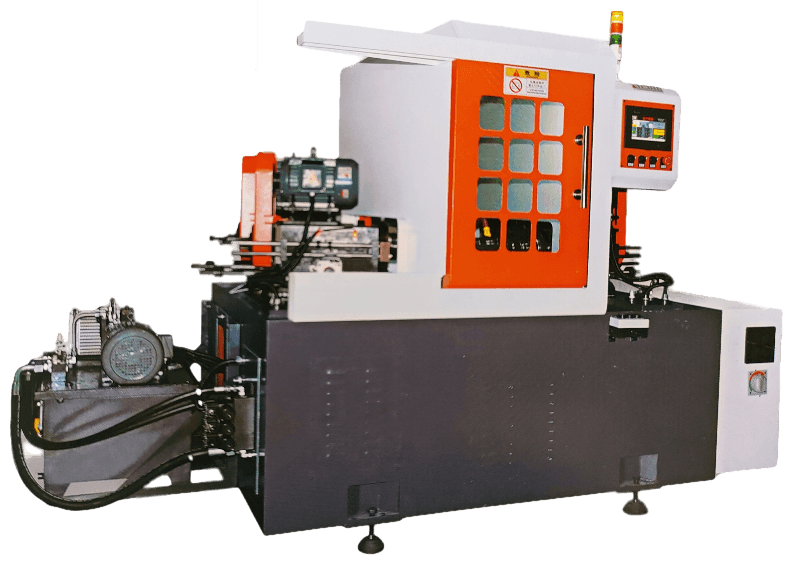
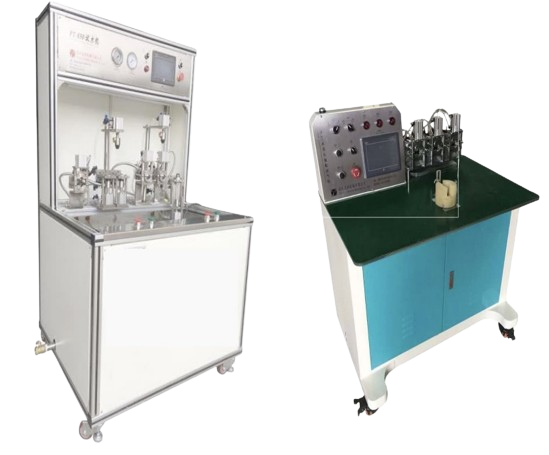
WATER LEAKAGE TESTING MACHINE
A water leakage testing machine is a device or system designed to assess the integrity of a product or component by subjecting it to conditions that mimic water exposure and detecting any leakage.